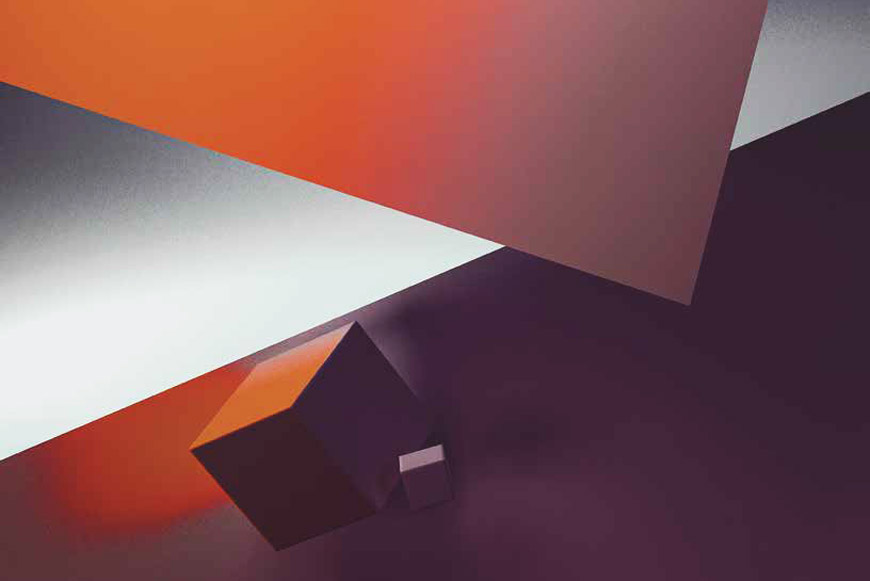
Цифровые технологии для изделий авиационно-космической отрасли
English
DIGITAL TECHNOLOGIES FOR AEROSPACE INDUSTRY PRODUCTS
Valery V. BARYGIN, Candidate of Technical Sciences, Ceo, OOO Relicom, Moscow, Russia, valery.barygin@relicom.ru
ABSTRACT. The creation of new generations of products in the aerospace industry is possible by applying a fundamentally new method of designing and manufacturing solid metal multilayer monocoque. A new additive manufacturing technology based on Russian patents is proposed.
Keywords: new technologies, monocoque, solid monocoque, multi-layer monocoque, additive technologies, digital technologies
ВВЕДЕНИЕ
Исторически сложилось, что при конструировании корпусов авиационной техники аэродинамическая оболочка изделия, обеспечивающая минимальное сопротивление внешней среде и требуемую подъёмную силу, опирается на внутренний силовой каркас, состоящий из поперечных шпангоутов и продольных лонжеронов и стрингеров. Такая конструкция аэродинамической оболочки на силовом каркасе с XX века именуется монококом (или тонкостенным монококом), что дословно переводится как «цельная раковина». До сих пор в массовом производстве изделий листы аэродинамической оболочки крепятся к силовому каркасу клёпкой, а в лучшем случае сваркой или склеиванием.
На сегодняшний день наиболее перспективной считается технология изготовления фюзеляжа и крыла самолёта из композитных материалов. Основными достоинствами конструкции из композитных материалов в сравнении с такой же конструкцией из металла считаются более высокая прочность, меньший вес, лучшая устойчивость к воздействию агрессивных сред.
Однако композитные технологии имеют и свои серьёзные недостатки. В сравнении с такой же деталью из металла деталь из композитных материалов обходится в несколько раз дороже. Технологически изготовление композитной детали имеет низкий процент автоматизации, поскольку многие процессы требуют ручного труда. Об экологичности композитных конструкций тоже можно спорить.
Но не рано ли отказываться от металлических конструкций в авиастроении?
Что, если бы появилась возможность практически без участия людей изготавливать фюзеляж самолёта требуемых размеров от носа до хвоста как цельную металлическую многослойную оболочку практически любой геометрии, переходящую изнутри в силовые элементы – без клёпки, сварки, склейки или соединительных элементов? Крыло, изготовленное таким же способом, можно соединить посредством фланца – и планер готов. Причём имеется возможность изготовить не традиционный каркас из шпангоутов, лонжеронов и стрингеров, а создать его в виде плетения силовых элементов под разными углами.
Существует область аддитивных технологий, которой уделяется недостаточно внимания. Специфичность её в том, что при наплавлении изделия используется не металлический порошок, а металлическая проволока определённого сплава и диаметра. Это направление имеет ряд преимуществ перед порошковыми технологиями.
ТЕХНОЛОГИЯ НЕПОСРЕДСТВЕННОГО СПЛАВЛЕНИЯ
Аддитивные технологии широко известны в мире и практически реализованы многими фирмами. Однако развитие аддитивной технологии изготовления изделий из металлов сконцентрировано на порошковой 3D-печати. Изделия относительно небольших размеров наплавляются из различных по составу и дисперсии порошков. Достигнуты впечатляющие успехи в создании металлических функциональных деталей для различных областей техники, например элементы конструкции ГТД из титановых, алюминиевых и других сплавов. В основном законодателями и держателями патентов в этой области являются американцы.
Однако существует область аддитивных технологий, которой уделяется недостаточно внимания. Специфичность этой области состоит в том, что при наплавлении изделия используется не металлический порошок, а металлическая проволока определённого сплава и диаметра. Это направление имеет ряд преимуществ перед порошковыми технологиями. Например, плотность, пористость изделия более предсказуема. Если процесс наплавления идёт в инертной среде, то захватываемые молекулы газа меньше оказывают влияние на качество изделия. Во многих случаях не требуется строгий контроль высоты наплавляемого слоя. Процесс наплавления проволокой работает и за пределами земной атмосферы.
За рубежом исследованием технологии, позволяющей создавать металлические функциональные детали и конструкции способом электронно-лучевой плавки проволоки (Electron Beam Additive Manufacturing (EBAM) Technology), занимается в NASA компания x3D Group (см. схему, рис. 1) при финансировании DARPA (Агентство передовых оборонных исследовательских проектов), Boeing, Lockheed Martin, GE, Pratt & Whitney.
Рис. 1. Схема работы способа EBAM
Работы, ведущиеся в этом направлении за рубежом с участием ведущих производителей авиакосмической техники, имеют очевидную перспективу стать тем заделом, который позволит создавать не только функциональные детали для высокотехнологичной техники, но и цельные конструкции с прорывными техническими показателями.
В нашем распоряжении сегодня есть основа, на которую можно опереться для организации работ по разработке конкретных технологических решений в этой области.
Эта основа – российские патенты RU2563063 и RU149949 на способ изготовления и устройство для изготовления многослойной монококовой конструкции в виде единой непрерывной оболочки [ 1, 2 ], патент RU2609571 на способ многослойного наплавления монокока [ 3 ]. Далее новую технологию изготовления многослойных монококов условно можно называть «технология непосредственного сплавления» (ТНС).
Рис. 2. Схема работы способа ТНС
Запатентованный в России способ (см. схему, рис. 2) более прогрессивен, чем американский.
Развитие ТНС позволит России не только наверстать упущенное, но и стать лидером в производстве многослойных монококовых конструкций как в условиях земной атмосферы, так и за её пределами. Прогрессивность российского способа заключается в следующем:
1. Использование электронно-лучевой плавки проволоки (EBAM) с целью изготовления функциональных деталей и конструкций ориентировано в основном на его применение в открытом космосе, если речь идёт о крупногабаритных конструкциях. Применение этого способа в условиях земной атмосферы потребует создания вакуумной камеры огромных размеров, что является дорогостоящим и технически сложно реализуемым проектом.
Применение лазерной наплавки проволоки в ТНС более универсально и не требует вакуумной камеры. В условиях земной атмосферы достаточно обычной промышленной вытяжки и ограждения от лазерного излучения.
2. В способе EBAM осуществляется полное плавление проволоки. Это приводит к трудно контролируемому процессу формирования детали, изготавливаемой согласно цифровой модели, и весьма неровным сформированным поверхностям.
В ТНС оплавляется лучом лазера лишь область непосредственного металлургического сплавления проволоки и конструкции. Это позволяет лучше контролировать формирующуюся конструкцию, расходовать меньше энергии и получать более качественную внешнюю и внутреннюю поверхность, что, соответственно, потребует меньше финишных технологических операций.
Реализация ТНС для применения в условиях земной атмосферы и для открытого космоса потребует проектирования разного типа технологической оснастки.
Предполагается, что для условий земной атмосферы технологическая оснастка позволит изготавливать многослойные монококи требуемой длины диаметром до 10 м с точностью до 0,15 мм, а в условиях открытого космоса – с характерными размерами, измеряемыми до нескольких сотен метров.
В технологии непосредственного сплавления лучом лазера оплавляется лишь область металлургического сплавления проволоки и конструкции. Это позволяет лучше контролировать формирующуюся конструкцию, расходовать меньше энергии и получать более качественную внешнюю и внутреннюю поверхность.
ВАЖНЕЙШИЕ ПРИНЦИПЫ ТНС И ЭКСПЕРИМЕНТАЛЬНАЯ УСТАНОВКА
1. Возможность изготавливать металлополимерные крупногабаритные многослойные монококи как цельные конструктивы.
2. Практически полная автоматизация производства.
Рис. 3. Экспериментальное технологическое оборудование для изготовления многослойных монококов
В качестве экспериментального технологического оборудования (рис. 3) предполагается использовать стандартное высокоточное оборудование, интегрированное в России для автоматизации производственных процессов.
Всё высокоточное оборудование (включая сервоприводы поддержки изделия) будет управляться единой электронной системой и будет смонтировано и настроено на производственном участке российским интегратором. Необходимое обучение может быть проведено на учебной базе в Москве или, при необходимости, на производственном участке. Технологическое оборудование должно иметь достаточное ограждение исходя из требований безопасности работы с лазерным оборудованием. Размеры технологической площадки должны быть достаточными. Так, для полномасштабного изготовления части корпуса вертолёта Ми-8 площадка должна быть не менее 15 м длиной и 10 м шириной.
Рис. 4. Экспериментальное технологическое оборудование для изготовления многослойных монококов
ВЫВОДЫ И РЕКОМЕНДАЦИИ
Потребность в крупногабаритных многослойных монококах – прочных, лёгких и дешёвых – в технике велика. Это – планеры самолётов, корпуса вертолётов, корпуса ракет, прочные корпуса глубоководных технических средств, кузова автомобилей, корпуса реакторов, а также крупногабаритные оболочки типа монокок различной формы, лежащие в основе специальной инфраструктуры на околоземной орбите: производственные, складские, жилые блоки, грузовые платформы.
Что позволит реализация ТНС?
1. Выйти на новый уровень прочностных характеристик всех изделий, в основе которых лежит монокок.
2. Значительно улучшить ТТХ изделий за счёт существенного снижения веса изделий и оптимизации конструкции.
3. Выйти на новый уровень надёжности изделий, поскольку удастся избежать человеческого фактора в процессе изготовления изделия.
4. Значительно снизить себестоимость изделий за счёт практически полной автоматизации производственного процесса, который может идти круглосуточно.
Реализация технологии непосредственного сплавления позволит выйти на новый уровень прочностных характеристик всех изделий, в основе которых лежит монокок.
Литература:
- Патент РФ 2563063. Способ изготовления многослойной монококовой конструкции в виде единой непрерывной оболочки / Барыгин В. В.; заявл. 08.11.2013, опубл. 20.09.2015, бюлл. №26.
- Патент РФ 149949. Устройство для изготовления монококовой конструкции в виде единой непрерывной оболочки / Барыгин В. В.; заявл. 10.04.2014, опубл. 27.01.2015, бюлл. №3.
- Патент РФ 2609571. Способ многослойного наплавления монокока / Барыгин В. В.; заявл. 22.06.2015, опубл. 02.02.2017, бюлл. №4.
References:
- Barygin V. V. Sposob izgotovlenija mnogoslojnoj monokokovoj konstrukcii v vide edinoj nepreryvnoj obolochki. Patent RF no. 2563063 (2013).
- Barygin V. V. Ustrojstvo dlja izgotovlenija monokokovoj konstrukcii v vide edinoj nepreryvnoj obolochki. Patent RF no. 149949 (2014).
- Barygin V. V. Sposob mnogoslojnogo naplavlenija monokoka. Patent RF no. 2609571 (2015).
© Барыгин В. В., 2021
История статьи:
Поступила в редакцию: 24.02.2021
Принята к публикации: 22.03. 2021
Модератор: Гесс Л. А.
Конфликт интересов: отсутствует
Для цитирования: Барыгин В. В. Цифровые технологии для изделий авиационно-космической отрасли // Воздушно-космическая сфера. 2021. №2. С. 76-83.